What is conveying equipment and how does it work?
What is conveying equipment?
Conveying equipment is a vital component of many industrial and commercial processes. It refers to the machinery and systems used to transport materials, goods, or products from one location to another within a factory, warehouse, or distribution center. The use of conveying equipment has revolutionized the way goods are moved, increasing efficiency and reducing manual labor.
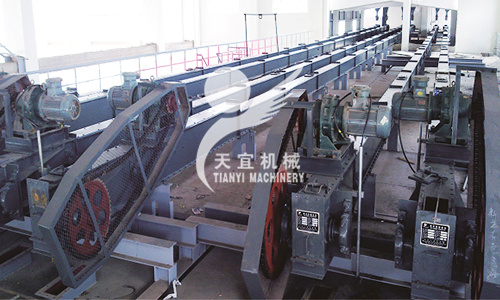
Types of Conveying Equipment:
1. Belt Conveyors:
Belt conveyors are the most commonly used type of conveying equipment. They consist of a continuous belt made of rubber, canvas, or metal and are driven by motorized pulleys. Belt conveyors are versatile and can handle a wide range of materials, including packages, boxes, and bulk materials.
2. Roller Conveyors:
As the name suggests, roller conveyors consist of a series of rollers mounted on a frame. The rollers rotate as products or materials move along them, reducing friction and making it easier to move heavier loads. Roller conveyors are commonly used in warehouses and distribution centers for order fulfillment, packaging, and shipping applications.
3. Screw Conveyors:
Screw conveyors are a type of equipment that uses a rotating helical screw blade, known as an auger, to move materials. They are suitable for handling various materials, including bulk solids, liquids, semi-solids, and granules. Screw conveyors are commonly used in food processing, agriculture, mining, and wastewater treatment industries.
4. Pneumatic Conveyors:
Pneumatic conveyors use a stream of pressurized air to move materials through a closed pipe system. They are ideal for handling dry and powdered materials, such as flour, chemicals, and cement. Pneumatic conveyors are known for their flexibility, efficiency, and ability to transport materials over long distances.
5. Bucket Elevators:
Bucket elevators are used to move bulk materials, such as grains, coal, or minerals vertically between levels of a facility. They consist of a series of buckets attached to a chain or belt and are designed to scoop up materials from a lower level and deposit them at a higher level.
6. Vibrating Conveyors:
Vibrating conveyors use vibrations to move materials. They are particularly useful for moving delicate or sticky materials that may get stuck on other types of conveyors. Vibrating conveyors are commonly used in food processing, mining, and recycling industries.
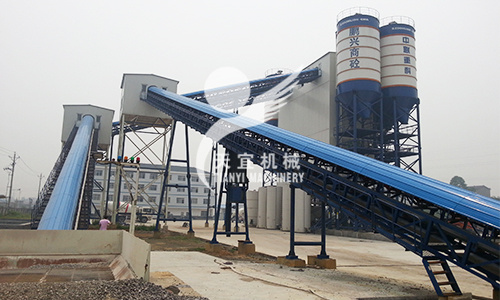
Functions of Conveying Equipment:
1. Transportation:
The primary function of conveying equipment is to transport materials from one location to another. This can include moving materials from a loading dock to a storage area or from one stage of a production line to the next.
2. Sorting:
Conveyors can also be used for sorting materials based on their size, shape, or type. This is particularly useful in the shipping and logistics industry, where packages and parcels need to be sorted quickly and accurately.
3. Accumulation:
Conveying equipment can also be used to accumulate products or materials, allowing them to build up in a specific area before being moved to the next stage. This is commonly seen in warehouses and distribution centers, where products are sorted and accumulated before being packaged and shipped.
4. Storage:
Some types of conveying equipment, such as bucket elevators, can also be used for temporary storage of materials. This allows for efficient use of space and can help facilities keep up with production demands.
How Conveying Equipment Works:
The working principles of conveying equipment will vary depending on the type of equipment being used. However, there are some general steps that most conveying equipment follows to move materials from one location to another.
1. Loading:
The first step in the process is loading the materials onto the conveyor. This can be done manually or through automated systems, depending on the type of conveying equipment.
2. Transportation:
Once the materials have been loaded onto the conveyor, they are moved along by the motion of the conveyor belt, roller, or screw. This can be done using electric motors, pneumatic systems, or gravity.
3. Sorting/Accumulation:
As the materials move along the conveyor, they may pass through sorting mechanisms or accumulate in designated areas, depending on the function of the conveyor.
4. Unloading:
Finally, the materials are unloaded at their designated location, such as a storage area, packaging station, or loading dock.
Benefits of Conveying Equipment:
1. Increased Efficiency:
Conveying equipment can significantly improve the efficiency of material handling processes. By automating the movement of materials, it reduces the need for manual labor and speeds up production cycles.
2. Cost Savings:
With fewer manual labor requirements, companies can save on labor costs. Additionally, the use of conveying equipment can reduce the risk of product damage, resulting in cost savings for businesses.
3. Improved Safety:
Using conveying equipment reduces the risk of accidents and injuries associated with manual material handling. This can improve workplace safety and reduce workers' compensation claims.
4. Better Product Quality:
Conveying equipment can help maintain the integrity and quality of products by reducing handling and preventing damage during transportation.
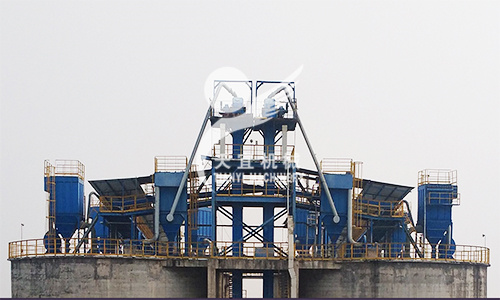
Tianyi Machinery is a high-tech enterprises, which specialize in designing & producing &installing conveying equipment, crush equipment and screening equipment.
The company is located in Yidu City,Hubei Province, which is involved in Yi Chang Three Gorges “half-an -hour” economic area and at the junction of Hubei, Sichuan and Hunan Provinces. It is only 50 kilometers far from the Three Gorges Dam & 20 kilometers apart from Three Gorges Airport. Besides, Jiao-liu railway and the Hu-rong freeway is crossing our city. Therefore, the transportation is pretty convenient for all of us.
Tianyi Machinery is mainly designs and produces related conveying equipment for electric power,metallurgy,chemical industry,cement and other industries. Especially in thermal power industry, coal transport, coal feeding and dry slag removal, limestone receiving system in limestone slurry preparation in flue gas desulfurization system, limestone powder transportation in dry desulfurization system; Raw material transportation, process dust collection system, waste heat boiler high temperature slag transportation, waste incineration power plant high temperature bottom slag and coal economizer high temperature ash and slag transportation have unique advantages.
Related Issues:
What are the key components of conveying equipment?
The key components of conveying equipment include:
Conveyor belt/chains: This is the main part of the equipment that carries and moves the materials or products.
Drive unit: This provides the power necessary to move the conveyor belt/chains.
Rollers/idlers: These components support the weight of the materials or products and help to guide them along the conveyor.
Motors/reducers: These provide the power to drive the conveyor belt/chains and can be adjusted to control the speed of the conveyor.
Belting/material handling accessories: These are used to modify and support the conveyor belt or chains to meet the specific needs of the application.
Control systems: These components ensure that the conveyor operates smoothly and efficiently and allows for adjustments to be made as needed.
How does conveying equipment improve efficiency in manufacturing and logistics processes?
Conveying equipment improves efficiency in manufacturing and logistics processes in the following ways:
Increased speed of material handling: Conveyors can move materials and products faster than manual methods, reducing the time it takes to complete tasks and improving overall productivity.
Reduction in labor costs: Conveying equipment eliminates the need for manual handling of materials, reducing the number of workers required and allowing them to focus on other tasks.
Improved accuracy: Conveyors can be designed to accurately move and position materials, reducing errors and minimizing the risk of damage to products.
Space utilization: Conveyors can be designed to fit into tight or confined spaces, maximizing the use of available space in a facility.
Lower risk of workplace injuries: Manual handling of heavy or bulky materials can lead to injuries for workers, whereas conveying equipment handles these tasks safely and efficiently.
What are some common types of conveying equipment and their applications?
Some common types of conveying equipment and their applications include:
Belt conveyors: These are used to transport materials or products on a continuous belt. They are commonly used in manufacturing and distribution facilities.
Chain conveyors: Similar to belt conveyors, these use chains instead of belts to move materials or products. They are often used for heavy-duty or high-volume applications.
Roller conveyors: These utilize rollers instead of a continuous belt or chain to move materials or products. They are commonly used for moving objects with flat and stable bottoms, such as boxes or totes.
Gravity conveyors: These use gravity to move materials or products along a downward slope. They are generally used for light-duty applications and do not require power.
Screw conveyors: These use a rotating screw to move materials along a tube or trough. They are often used for bulk materials, such as grains, powders, or liquids.
Pneumatic conveyors: These use air pressure to move materials through a network of tubes. They are commonly used for handling fine powders or granular materials.
Can conveying equipment be integrated with other automated systems, such as robotics, in modern production facilities?
Yes, conveying equipment can be integrated with other automated systems, such as robotics, in modern production facilities. This integration allows for a seamless transfer of materials or products from one process to another, increasing efficiency and reducing the need for manual labor. For example, sensors can be used to signal when materials are ready to be picked up by a robotic arm and placed on a conveyor for transport to the next stage of production. This integration also allows for data sharing between systems, leading to improved decision making and optimization of processes.